What is warehouse slotting? At its most basic, warehouse slotting is inventory management. You will need to analyze the inventory data for your business, categorize what you have in stock, and organize it in proper storage containers to achieve warehouse slotting optimization. Let’s explore some of the best warehouse slotting practices.
Warehouse Slotting Benefits
Warehouse slotting is a type of inventory management that increases efficiency. You essentially organize the inventory in a way that makes sense for your team. Slotting in warehouse management means establishing an organizational system that maximizes the overall layout, including all shelves and pallets.
Why should you care about warehouse slotting optimization? Here are a few reasons:
Optimize Warehouse Space
It’s unlikely that all of your inventory will be in similar boxes. Some will be large, while others will be smaller. Some will need to be handled with care because they’re fragile. A vital part of warehouse slotting strategies and optimization is to sort items into similar categories and maximize their organization.
When you do this, you’ll find that you have significantly more space and will be able to increase the amount of slotting in the warehouse that you can do.
Another advantage of the additional space is that you won’t need more space. The ability to pack more items into a smaller space will result in you not needing to rent or buy another one. That’s less money that you’ll be losing in overhead and more money in your pocket.
Improve Warehouse Efficiency
Another component of warehouse slotting optimization is efficiency. If your warehouse workers have to go to the back of the building to get popular items, they are wasting time. If they have to go from one part of the warehouse to another to complete orders while picking, that is another waste of time.
When using an optimal warehouse slotting organization, you can put everything a worker needs in logical places. They’ll be able to complete orders quickly; and efficiently. A warehouse team that works efficiently will get more orders out than one which isn’t.
Faster fulfillment will mean a better relationship with customers. After all, would you rather receive items from a warehouse that completes orders promptly? Or one that has a significant lag time?
Reduce Picking Errors
It’s all too easy for warehouse pickers to make a mistake when organizing. When using warehouse slotting optimization, you can minimize those mistakes. By placing items together and not scattered about, warehouse workers will find them easily. They will also find them quickly. Warehouse workers will be able to reduce redundancy and ship more orders.
Reduction in errors will mean that you’ll spend less time later attempting to fix them, and smoothing over troubles with your clients.
Improving Warehouse Flow
Your warehouse will be full of employees, each of them working on different orders. With warehouse slotting, you can eliminate competition for space and resources. Sometimes one employee will block another from reaching the product, but if you arrange your warehouse efficiently, everyone will have more access.
Additionally, when you watch your flow, you will be monitoring employee safety. You don’t want your workers to need to be constantly navigating large and cumbersome boxes. You also don’t want them to have to go around forklifts or other hazards if it’s not necessary.
Maintaining Warehouse Inventory Integrity
Proper warehouse slotting will ensure that fragile items are kept safe and that other products aren’t damaged by employees trying to access them. Accidents happen, but utilizing warehouse slotting strategies to organize your products can prevent them from being damaged. You may want to invest in durable containers to store your products, such as corrugated plastics.
Your customers will be glad to receive items in the best possible condition, and you’ll be happy when you experience less product loss due to damages.
Warehouse Slotting Optimization Techniques
To begin the process involves a significant amount of inventory data. It is beneficial to start with at least a year’s worth, including seasonal changes and possible inventory growth.
If you have a warehouse management system, you may be able to access inventory slotting software. The software may be accessible, or you might need to have it added as an additional module.
If you don’t have a system, one can be purchased. If not, you can hire a third-party consultant to review your warehouse and the current systems. If you’re inexperienced with this process, it can be helpful to have an expert on hand to assist you.
Whatever method you choose, the data collected should be the following:
- SKU picking methodology
- The number of pallets, cartons, and individual pieces
- SKU hits
- Pick quantities
- SKUs picked together
- SKU sizes and weights
- Total SKU, reorder points, and quantities
- Level items are stored.
- Special storage requirements
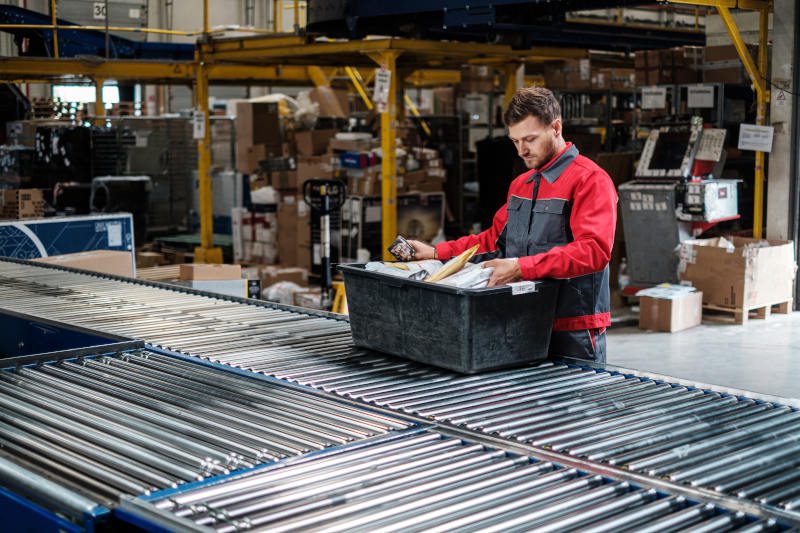
Item Level and Packaging
Item level and packaging are critical components of warehouse slotting. You should place heavier items on lower shelves. Doing this will prevent injury to your workers. It will also maintain the integrity of your shelving. Keeping lighter products on mid-level to higher shelving is safer for workers.
You will want to keep the harder-to-move items away from items frequently picked. Warehouse slotting strategies that prioritize products will result in an efficient system. Workers will be able to select items quickly. Products that need a forklift to move will be easier to access, and workers will be able to obtain the items without getting in the way.
Packing is important. You don’t want to package your items in something that will break apart. Instead, you should look into sturdy containers, such as plastic.
You may want to look into a company that focuses on warehouse slotting. They can assist with kitting your warehouse out and improving your general organization.
Warehouse Velocity
Velocity is about how fast items move in and out of your warehouse. You should not keep the high-velocity product in the back of your warehouse. You will waste your workers’ time. It will also lead to lag times in efficiency. Keep high-velocity products where your workers can quickly access them.
Slower movers can stay in the back, where they will be out of the way.
You can determine which is which by listing all SKUs over some time. Thirty days is a standard time, though you may go shorter or longer depending on your needs. From there, you can determine your ‘ABC’ slotting.
The top 50% are the items with the most line orders, those will be your ‘A’ slot products. The next 25% is your ‘B’ products. The last 25% is your ‘C’ products. Items that were ordered during the year but not during the time you did inventory are classified as ‘D’.
Your ‘A’ products can be placed the closest to the picking action in your warehouse. These will be your high-velocity products. ‘C’ and ‘D’ products will be placed in the back, accessible when needed but out of the way of the regular flow of your warehouse.
It is to your benefit to not just get the data from the last thirty days. If you can go back further, you will be able to get a better picture of the future.
Seasonality
Seasonality is important to keep in mind. It might make sense to keep the forward picking point of your warehouse stocked with Christmas items in November and December, but less so during March. You should make sure to make these critical adjustments.
Specialty Storage
When you are working on your warehouse slotting organization, you should be taking into account specialty items. This may require you to have certain facilities at your warehouse.
Cold Storage
This would be anything perishable. Refrigerated items would need to be chilled, and frozen items would need an appropriate freezer space handling.
Hazardous Storage
Flammable liquids and chemicals are kept in separate, specially designed storage units and secured by a lock and key. Items like oxygen tanks and propane cylinders are stored in large cages so there’s less chance of them being knocked over.
Archive Storage
This is for important documents and data used by companies. It’s also prominent in the medical community as they make the shift from paper charts to digital.
Warehouse Organization Is Key
An organized warehouse is a happy warehouse. Your workers will thrive in their ability to be productive. Your customers will be happy when they receive their goods on time. And you’ll be far less stressed when both of those things are happening thanks to your warehouse slotting strategies.
At the end of the day, it’s going to result in increased monetary gains for your company. And that’s something that every warehouse manager looks forward to. If you’re struggling, it may be helpful to look for a warehouse organization to help you.
Improve Efficiency With Slotting in Warehouses
Slotting in a warehouse can be a challenge. It may feel like an overwhelming challenge to get your warehouse slotting optimized. But it’s entirely doable if you start small. Utilize warehouse managing systems to help you, or hire someone to take on the task.
Monitor your inventory to assess what’s coming in and going out. Assign an ABC system so that you can organize your warehouse and control the flow of goods coherently.
Look through the products that you’re keeping in your warehouse and make sure that you’re storing them properly as well. Don’t store hazardous chemicals somewhere that they can be knocked over or accessed.
Always watch out for seasonality, it’s important to stay organized. If you’re ready to talk with one of our team members about how we can help improve your warehouse slotting best practices, contact MDI today.